What Constitutes a Successful QMS?
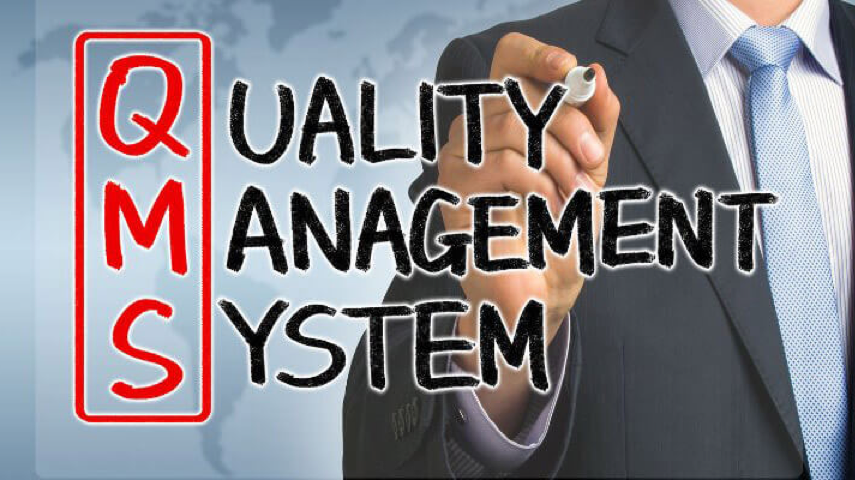
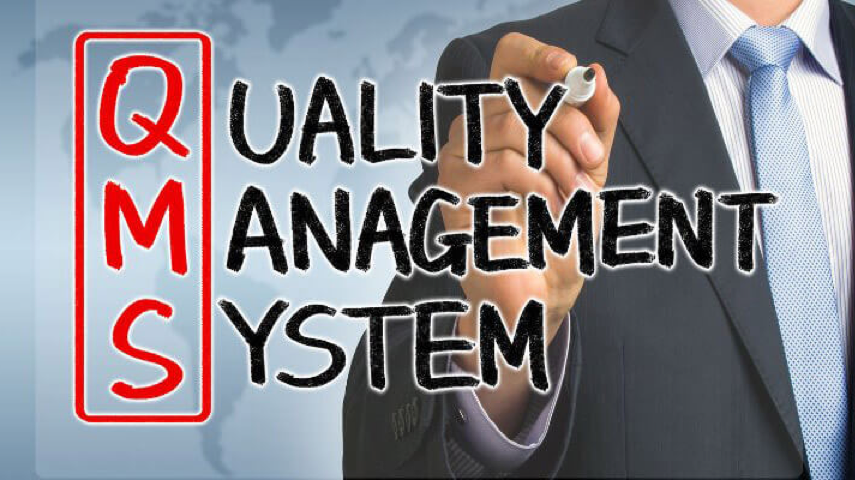
It has been a little more than a week since I attended the ISO 9000 World Conference in Nashville, TN. The conference was full of great people and great companies. I loved hearing what everyone had to say about the revisions to ISO, general QMS standards, and what changes people are implementing to become more efficient in their operations.
Upon my return home to Oklahoma City, I was immediately met with the opportunity to develop our very own Quality Management System in our newest software platform, PERFEQTA. This new opportunity forced me to question โWhat constitutes a successful QMS?โ
A successful QMS consists of written and controlled procedures. These procedures are the basis for auditable events performed by either external or internal audit teams. An effective QMS will identify key process steps and prevent most failures before they occur. It will protect your supply chain, your brand, and most importantly, your consumers. This is something that is understood and widely accepted among organizations who adopt strict Quality Management policies.
There are several steps involved in creating a solid QMS. These include the following:
- Statistical tools and control plans.
- Failure modes and effects analysis of quality standards for the specific industry.
- Systems validation protocols.
- Current good practices.
Putting all of these steps to work, and having them work properly together, is the most effective way to achieve the best results. The secret to any and all quality/process improvement efforts is employee ownership. Employees must believe in the change process and have ownership in the process being changed. For an employee to believe in the change and effectively use the system, this ownership must come from the top and trickle down. To create this ownership, it has become evident to many a quality professional that partnering with the lean and Six Sigma initiatives, as opposed to trying to โownโ them, can produce significant results.
To create a streamlined and efficient quality management system, flexibility is needed to adapt to dynamic changes in products and markets. A successful QMS, designed with flexible workflow and routing capabilities, is well suited for this purpose. In addition, the ability to coordinate and collaborate across multiple areas and external resources is key to successful change implementation. It must be a system that can be used across the board and be fully integrated into a business.
If you are interested in learning more about how our platform stacks up against a consensus of industry standard QMS software, take a look at our website perfeqta.io or the comparison chart we just posted on our PERFEQTA LinkedIn page.
Originally posted to LinkedIn on April 6, 2017 โ To view original post click here