Mastering Non-Conformance Reports: Tips for Success
Nonconformance reports (NCRs) are a crucial element in quality control, helping organizations identify and address issues that could impact product or service quality. In this blog post, we will cover everything you need to know about NCRs- from what they are and why they are important in ISO standards to how to identify nonconformities and take action to prevent them. We will also discuss the consequences of not addressing nonconformities and provide examples of effective NCRs. Additionally, we will offer best practices for writing a great NCR and explore how digital nonconformance management tools can help improve compliance. Whether you’re an ISO auditor or simply looking to improve your organization’s quality control processes, this post will provide valuable insights into avoiding costly errors with NCRs.
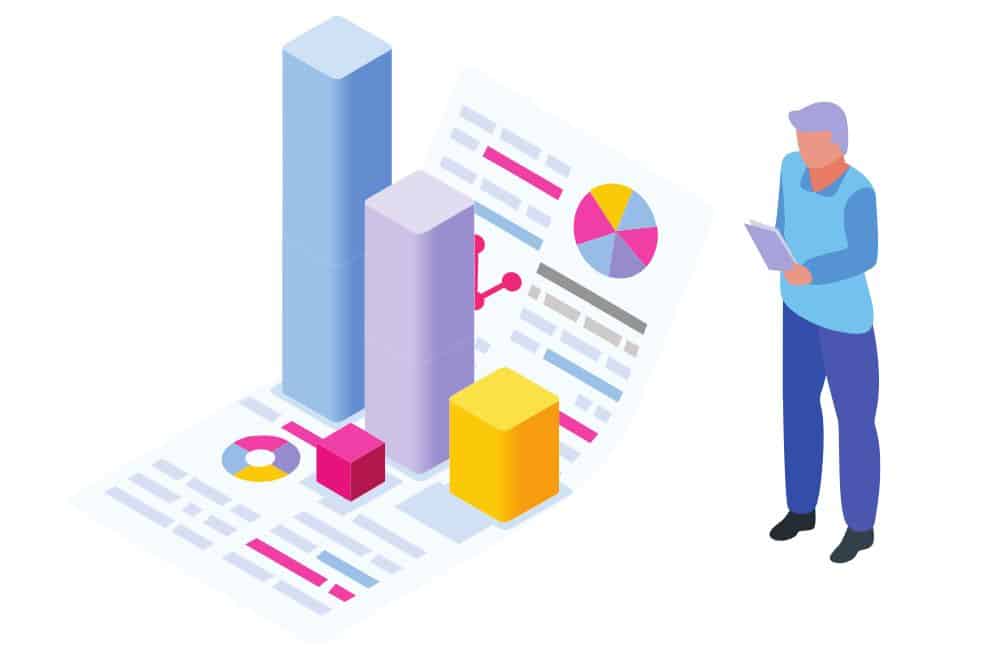
What is a Nonconformance Report?
A Nonconformance Report (NCR) is a report that documents when something does not meet quality standards. It’s used across industries to identify and correct quality issues, including details on the impact and corrective actions taken. Proper handling of NCRs can prevent errors and improve quality control processes.
Importance of Nonconformance Reports in ISO Standards
Nonconformance reports (NCR) play a crucial role in maintaining quality standards of the highest order. These reports help in identifying and addressing issues related to various processes or products that may arise from time to time. Such reporting effectively prevents the occurrence of costly errors that might have a profound impact on the overall quality control regime of an organization. Additionally, it helps such firms to improve their operational processes by avoiding the recurrence of non-conformities while demonstrating a firm commitment to improving its quality management system continuously.
When to Issue a Nonconformance Report?
Nonconformance reports must be issued whenever a product or service fails to meet specified requirements and should be done promptly. These reports should provide comprehensive details on the nonconformity, its consequences, and the corrective measures taken. Issuing such reports can prevent further quality issues and enhance the overall quality of the product or service.
Who Can Issue a Nonconformance Report?
Anyone who identifies a nonconformance issue can issue a Nonconformance Report, including employees, inspectors, auditors, or customers. However, the person issuing the report must have adequate knowledge and authority to identify and report the nonconformity. Prompt handling of Nonconformance Reports is crucial, and corrective action should be taken to resolve them.
Tips for Writing an Effective Non-Conformance Report
Avoid writing a non-conformance report when it is the first time that the subject has been encountered. This will be more convincing to management.
It is important to include as much information in the report as possible. The report should be structured and easy to read, both for the reader and management.
The recommendation of a person who can make an independent judgment on this issue should also be included in the report.
Include copies of all documents that support your case and show how you arrived at your conclusions about what happened. If there are supporting documents, they should also be attached to the report so that management will not have to wait for them before acting on your recommendations.
If you do not know where exactly you were wrong, it is essential to seek assistance from a subject-matter expert or a supervisor before drafting the report. This will ensure that your report accurately reflects the nonconformance issue and its impact.
Use clear and concise language in your report, avoiding technical jargon when possible. The purpose of the report is to communicate the issue and its potential consequences clearly and effectively to management.
Lastly, be specific about the corrective actions that should be taken, including who is responsible for implementing them and by what deadline. This will help prevent similar issues from occurring in the future and demonstrate a commitment to quality improvement.
How to Identify Nonconformities
To effectively identify non-conformance occurrences in any product or service specification setting, consider understanding the applicable product or service requirements and specifications. Conducting regular audits and inspections can effectively aid in identifying potential deviations from set standards, while proper employee training can encourage the timely identification of such irregularities. Developing a clear process for documenting nonconforming parts as well as addressing the root cause of the nonconformance would assist in preventing possible future occurrences. Finally, a continuous review of such processes will maintain quality conformance levels.
1. Conducting Internal Audits
To prevent costly errors and ensure compliance with regulations, conducting internal audits is essential. Reviewing processes, procedures, and documentation to identify nonconformities before they become major issues is an effective way of staying on top of potential non-conformities. Regular internal audits can also assist organizations in taking corrective action in a timely manner.
2. Utilizing Nonconformance Management Software
Streamlining the identification and resolution of non-conformities is crucial to avoid costly errors. The utilization of nonconformance management software tracks ncr occurrences and assigns corrective action while monitoring progress toward resolution. Moreover, it reduces the risk of defects with an efficient central system for managing quality control. When selecting a quality management system to ensure effectiveness in managing non-conformities, consider user-friendliness in customization options and integration capabilities.
Understanding and Analyzing Nonconformities
To avoid costly errors with non-conformance reports, it’s crucial to understand and analyze nonconformities effectively. Major and minor non-conformities must be differentiated, root cause analysis must be performed, and disposition for nonconformities must be determined before creating a Corrective and Preventive Action (CAPA) plan to address the non-conformance. Monitoring the effectiveness of corrective actions and documenting the non-conformance investigation help in detecting potential problems. This ultimately leads to a quality management system that ensures compliance with quality standards.
1. Differentiating between Major and Minor Nonconformances
It’s crucial to differentiate between major and minor non-conformities by understanding their severity. Major non-conformities demand immediate attention to comply with regulations or standards. On the other hand, minor non-conformities may not have a significant impact but should still be addressed. By properly classifying and analyzing them, organizations can identify the root causes of the problem and take corrective actions. Effective management of non-conformance reports helps in reducing costs associated with quality control and compliance issues.
2. Root Cause Analysis Process
The Root Cause Analysis Process plays a crucial role in addressing non-conformance reports effectively. This systematic process includes identifying problems and gathering relevant data. Further analyzing this data with tools like fishbone diagrams or brainstorming leads to identifying the root cause of non-conformities. Once identified, corrective actions are developed accordingly. By adhering to this process with additional strategies like 5 Whyโs, organizations can improve their quality management system and prevent possible occurrences in the future.
3. Determining Disposition for Nonconformities
After identifying a non-conformance report in a quality management system like ISO standards and conducting root cause analysis using objective evidence such as audits or corrective actions (CAPA), it is essential to determine its severity through effective non-conformance reporting and decide on the appropriate action. The disposition decision should be based on factors such as risk, the potential impact on non-conforming parts or medical devices regulated by FDA compliance, or other quality standards like documentation of work instructions or calibration date. Options for disposition may include rework, repair, or scrap depending on the level of severity of minor or major nonconformities in NC reports. It’s crucial to document the decision and communicate it to relevant stakeholders, including team members and auditors.
Taking Action to Prevent Nonconformities
Taking action to prevent non-conformities is critical for effective quality management. Proactive measures like regular audits and employee training can reduce errors. Utilizing technology can streamline processes and increase efficiency. Additionally,
creating a corrective and preventive action plan is crucial to limit the repetition of issues. Proper documentation of investigations is important for internal calibration date setting. Overall, adherence to standards and regulations can enhance stakeholder trust.
1. Creating Corrective and Preventive Action (CAPA) Plan
To prevent non-conformances in the future, creating a Corrective and Preventive Action (CAPA) plan is imperative. The initial stage involves identifying potential causes of non-compliance, followed by developing an action plan to address underlying issues. Furthermore, successful implementation demands clear timelines and responsibilities at each step of the process. Finally, regular review & monitoring are essential for effectiveness.
2. Monitoring Effectiveness of Action
Effective Non-Conformance Reports require adherence to ISO standards and a proactive approach toward Quality Controls. To maintain compliance with objectives and standards laid out in Quality Management System specifications, stakeholders must identify and address the Root Causes of Non-Conforming products through Corrective Actions (CAPA). Continuous monitoring and retrospective documentation through internal audits help identify potential problems with calibration dates or work instructions. Utilizing Nonconformance Management Software helps streamline processes and reduce human error.
3. Documenting Nonconformance Investigation
Documenting a nonconformance investigation requires recording all details related to the issue, root cause analysis, corrective actions implemented, and follow-up measures. Comprehensive documentation provides valuable insights for future process improvements and ensures compliance with regulatory requirements. By conducting a separate investigation and calibration of dates for non-conforming parts, effective non-conformance reporting can be achieved. Quality managers should ensure that team members follow the plan of action in order to prevent any potential recurrence of non-conformities.
Importance of Templates in Preparing a Nonconformance Report
Templates play a critical role in preparing effective non-conformance reports. Not only do they ensure consistency in format and content, but they also help save time while reducing errors. By customizing templates to meet specific industry or company requirements, stakeholders can capture vital data like root cause analysis and corrective actions taken. Regular reviews of the templates will also improve the effectiveness of non-conformance reporting processes.
What can Happen if Nonconformances are not Properly Addressed?
Ignoring nonconformances can result in expensive mistakes and safety risks, harming a company’s image and revenue. Neglecting them may lead to legal penalties and regulatory noncompliance. Addressing them correctly enhances quality control and prevents future problems.
Frequently Asked Questions on Nonconformance Reports
NCRs are an essential component of quality management systems like ISO. They allow companies to identify non-conformities, take corrective action and prevent similar defects from occurring again. The Frequently Asked Questions (FAQ) on NCRs provide a comprehensive understanding of the topic. They cover topics such as the importance of NCRs, common types of NCRs, best practices for creating and managing them, and how to prevent costly errors. Following these guidelines in creating an effective NCR system that incorporates root cause analysis and corrective actions taken can help organizations maintain high-quality standards.
How Digital Nonconformance Management Tools Can Help Improve Compliance
By using digital nonconformance management tools, organizations can automate the reporting process and reduce the risk of errors and delays. These tools provide real-time visibility into compliance metrics and help track non-conformances to ensure that corrective action is taken promptly. In addition to improving overall compliance posture to avoid costly penalties and fines, digital tools also streamline communication between different stakeholders involved in the nonconformance management process.
Case Studies and Examples of Effective Nonconformance Reports
Analyzing case studies and examples of effective nonconformance reports is critical in comprehending the impact of non-conforming products on an organization. By showcasing successful ncrs, businesses can learn how to create actionable reports that address the root cause of non-conformities. These case studies also highlight the significance of documentation, clear communication between stakeholders, and effective CAPA plans. Effective analysis helps businesses improve their QMS and avoid expensive penalties or fines.
Best Practices for Writing a Great Nonconformance Report
The best way to create an effective nonconformance report is by understanding its purpose. For a concise and clear report, use objective language while describing the issue and include supporting evidence such as photographs or test results. It’s crucial to add corrective actions that prevent future non-conformities. This helps in maintaining the quality standards of the products and services.
Key Takeaways from the 7 Essential Steps of a Nonconformance Report
It is crucial to follow an organized process when creating a non-conformance report. All details regarding the issue should be accurately documented, including observations, root cause analysis, and corrective actions taken. Establishing a system for tracking and monitoring non-conformance reports can ensure timely resolution, while continuous improvement can help reduce costs. Evidence-based findings should be provided while avoiding personal opinions or judgments. Corrective action must be taken or recommended to prevent future non-conformances.
What is ISO 9001 Non-Conformance?
ISO 9001 Non-Conformance refers to a situation where a product or service does not meet the required quality standards as specified in the ISO 9001 Quality Management System. A non-conformance report is then issued, which outlines the problem and suggests corrective action to be taken. This report is important for identifying areas of improvement within an organization’s processes or products. It helps organizations maintain compliance with ISO standards and ensures that customers receive high-quality products or services. By addressing non-conformance effectively, companies can improve their overall performance and reputation in the market.
Conclusion
In conclusion, nonconformance reports play a crucial role in ensuring product quality, customer satisfaction, and regulatory compliance. As such, it is essential to understand the process of identifying, analyzing, and preventing nonconformities to avoid costly errors. In addition, utilizing digital nonconformance management tools can streamline the process and improve compliance. If you need guidance on how to implement an effective nonconformance reporting system or want to learn more about our software solutions, book a free consultation today.